Overhead cranes play a key role in sheet metal fabrication operations. But they also pose significant hazards.
Companies should ensure their employees receive proper training to avoid accidents and other costly problems. The best way to do that is to choose a training program that meets OSHA and ASME safety standards. Click Osha Overhead Crane Training Requirements to learn more.
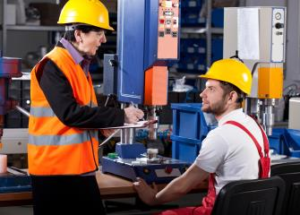
When it comes to overhead crane training, safety is paramount. During the training process, workers learn about the various hazards associated with cranes and the proper methods for operating them safely. This includes everything from the cab and pendant controls to the safety procedures that should be followed before and during critical lifts. The training program also teaches about best practices that extend beyond the crane cab and into the surrounding work area.
According to an OSHA study of over 270 accidents involving cranes, 70% could have been prevented with proper training. This is why it is imperative to take any training offered and complete all required certifications.
To ensure that your employees are properly trained to operate your cranes, make sure they receive training from an accredited training facility. In addition to classroom instruction, you should also consider having them complete practical and written exams. These exams should be conducted by an independent testing agency such as NCCCO.
Aside from training, you should consider upgrading your cranes to include features such as improved LED lighting that reduces power consumption and limits glare. This will allow your operators to see what they are doing better and minimise the risk of a mistake or accident.
It is the responsibility of management, or the company that owns the crane equipment, to provide training for people who are going to use it. The standard, ASME B30.2 offers a very extensive list of what should be covered in the training program, including but not limited to:
Load Calculations
Load calculations are an essential part of crane safety, and training programs play a key role in ensuring accurate load capacity and compliance with safety standards. Effective programs use hands-on exercises, simulations, and real-world scenarios to teach crane operators how to interpret load charts, assess environmental conditions, and make adjustments during lifting operations.
When determining the weight of an overhead load, it is important to consider both the rated and maximum capacity of the crane. The rated capacity is the amount of weight that the crane can safely lift, while the maximum capacity is the highest amount of weight the crane can lift under any circumstances. Both of these capacities are determined using a formula that factors in the weight of the crane itself, including the hoist and any other components.
Other variables that impact the crane’s capacity include the radius, configuration of movable parts, and environmental conditions like wind speed. Cranes are also classified based on their duty cycle, which determines how much the equipment can be used in a given period of time.
Another critical factor is the sling leg loading angle, which is determined by dividing the total load weight by the crane’s radius. This calculation is a simple trigonometry process that can be completed in-the-field by a skilled crane operator or rigger, and it can help to prevent overloading the sling leg.
Regular inspections and maintenance are vital for the safety of crane equipment. This is because these routine tasks ensure that all components of the crane are working correctly and are in good condition, reducing the risk of accidents or equipment failure. These inspections should be based on the manufacturer’s recommendations, industry standards, and any applicable regulations.
Pre-Operation Inspection
Overhead cranes are material-handling workhorses used across a range of industries. They are vital to the success of many operations, but they also pose potential hazards. Every year, crane accidents cause hundreds of injuries and dozens of deaths, as well as millions of dollars in property damage.
During general crane training, students learn how to perform a pre-operation inspection for various crane types. During the course, they will practice using specific checklists that help them ensure all the proper steps are taken to inspect the equipment and make sure it’s ready to use. They will also learn how to determine load limit tests. These are required after a crane is first commissioned, repaired or altered and should be conducted to ensure that the crane can safely lift its maximum load capacity. Students will be taught the step by step procedures for these tests and the determining factors that affect the crane’s ability to lift a load.
The course will also teach students how to inspect wire ropes and hooks for signs of wear or damage. They will learn the different kinds of hooks (eye hook, clevis hook, and swivel hook), their uses, and how to properly secure them. In addition, students will be taught about the requirements that wire rope must meet to pass inspections.
They will also be taught how to inspect a boom for signs of wear and damage, as well as the importance of the mechanical and electrical load brakes that are used in jib cranes. They will also be taught how to use the tag out system to lock out or tag out parts of a crane that have been inspected or replaced, so they cannot be used until they are untagged or re-inspected.
Post-Operation Inspection
As a final step, crane operators conduct a visual inspection and functional test of the hoist. They look at the equipment and its components for any signs of wear or damage, such as a hook latch that isn’t secured properly. They also inspect the mechanical and electric load brakes to make sure they’re working properly. This is important because a damaged hoist can cause injuries or damages to people, equipment, and buildings.
Crane accidents can be extremely costly. They cost companies money in regulatory fines, lost productivity, and a decline in employee morale. They can also cost lives if they’re not prevented with proper safety precautions, which is why it’s critical for companies to invest in overhead crane training for their employees.
During the training process, students learn how to read and interpret crane operation manuals. These include specifications for the crane model, government regulations, and hazards. Then, students are taught how to use inspection checklists correctly and document each inspection. This is important as OSHA requires monthly, periodic, and annual inspections of cranes.
Another important piece of training is how to perform a load limit test on a crane. These tests determine the maximum safe capacity of a crane for a specific job. These tests are required for new installations and after any repairs, modifications, or additions to the crane that could affect its capacity.
Finally, students are trained on the different types of wire ropes used in cranes and the requirements that must be met for a hoist to pass inspections. They are also taught the differences between the different types of hooks (eye, clevis, swivel) and how each should be used.
Maintenance
Overhead cranes require regular maintenance. If this isn’t done, it can lead to costly downtime, repair bills and the loss of production. Consistent training also ingrains safety protocols in operators, helping them instinctively follow these measures during normal operation. This reduces risk and saves companies money and stress in the long run.
Over time, wire ropes and pulleys can experience natural wear, which may cause reduced load capacity and greater strain on the crane structure. These issues can be spotted during daily inspections, which focus on looking for loose or damaged parts and ensuring the operation of safety tools such as limit switches. A more thorough inspection takes place at least once a month, and includes examining electrical connections, checking wire ropes, electric chains and sheaves, and inspecting structural components.
Crane safety also focuses on securing loads properly, and making sure that hoists and other mechanical parts are functioning correctly. Accidents can occur when these steps aren’t taken, such as if workers aren’t trained to operate the crane properly or if they fail to secure materials adequately.
A common error is overloading, which can be caused by a number of factors. Fortunately, this can be easily avoided by having well-trained operators and using accurate crane load charts.
Keeping up with the latest technology is another way to improve overhead crane safety. New advancements in crane equipment can increase load capacity, reduce the strain on wire ropes, and even improve efficiency. Investing in training for your operators and retrofitting older equipment with these newer safety features is an affordable, effective way to improve crane safety on your site. Contact a crane specialist today to find out how.